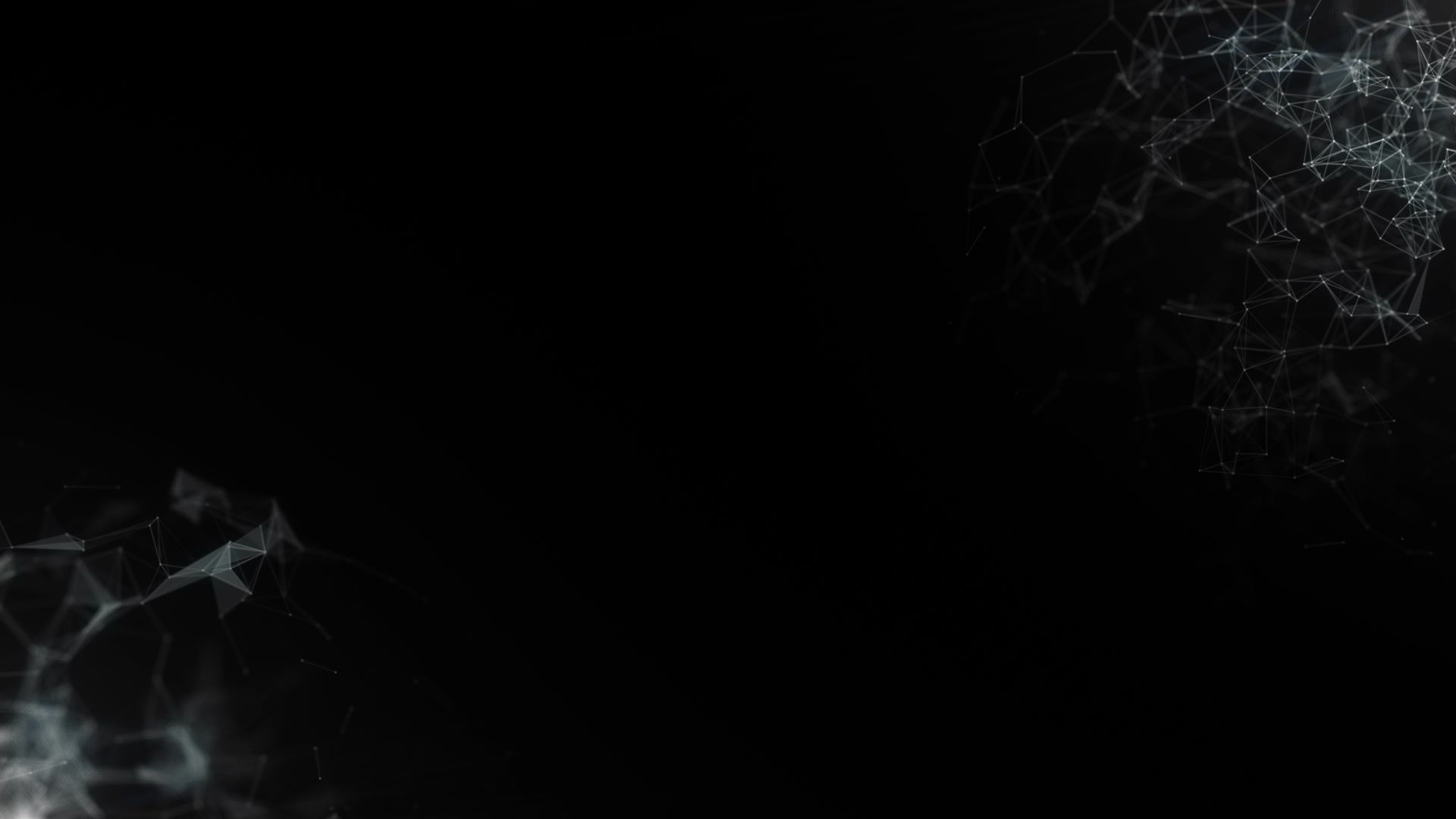

Senior Design Project
![]() Isometric View of Entire AssemblyHere you can clearly see the X, Y, and Z axis stepper motors. You can also see the lead screw/lead screw nut combination along the X-axis. | ![]() Side View of Entire Assembly | ![]() Top View of Lickspout Sub-Assembly |
---|---|---|
![]() Isometric ViewHere, you can see where the assembly is placed in the overall system, and where the lick-spouts' are placed relative to the mouse. | ![]() Pneumatic Valves and CircuitryThis image includes a rough view of the phidget microcontroller circuitry and the pneumatic solenoid valves. |
Automated Triple-Axis Retractable Lickspout Mechanism
This was an exciting project I did for my senior design project. We were contracted through the Allen Institute of Brain Science. The institute is dedicated understanding mammalian brain function when making high-order decisions in response to image features. We designed a system intended to assist mouse research related to advanced brain mapping technology. Our goal was to design a system with two independently retractable (at 5mm/50ms) "lickspouts" which would be used as a stimulus/response system for mice. The lickspouts had to be automated on all 3 axis to adjust for biological differences and be capable of repeatable extension placement within 50-micron, The system had to be able to move 10 mm each direction in 3-D space. The entire system also had to be quiet enough to not agitate the mice.
BRAINSTORMING PHASE:
It was decided that we would split the entire system into 2 sub-systems. One would be the lick-spout assembly, and the other would be a triple axis stage. The lick-spout assembly would take care of the retracting/extending of the lick-spouts and have a lick spout separation feature. The triple axis stage would give the lick-spouts the ability to be adjusted in 3-D space. I would be directly in charge of designing all models on SolidWorks, purchasing the necessary products/raw materials, and recording a bill of materials.
​
CONCEPT DESIGN PHASE:
​
I decided that aluminum would work fine for our system, as it is lightweight, corrosion-resistant, and fairly cheap for the amount we needed. I went through 7 Solidworks model iterations of the lick-spout sub-assembly and about 4 iterations of the triple axis stage sub-assembly. This process showed me an eye-opening realization of how many factors you have to account for when actually designing a product in which you have strict specifications and budget. I used a design for manufacture approach, which is a comprehensive approach to integrating the design process with production methods, materials, process planning, assembly/disassembly, testing, and quality assurance. This method helped me accomplish multiple tasks at once and greatly reduced the time required to complete the concept design phase. My first iterations turned out to be too complex and over-engineered. I evolved to understand that simplicity is best. I saw that it was very easy to overthink problems that could have had much easier solutions. Over-constraining the actuators was a large problem. After a few ridiculously complex iterations, a piece of angle iron and a 7/16" nut worked just fine. Persistence, a will to change my perspective, and keeping an open mind greatly helped me push through these struggles.
DETAILED DESIGN PHASE:
Now that we had a general model and idea of what our final product will look like, it was time to start nailing out specific details and buying products such as actuators, stepper motors, lead screws, and linear guide rails.
I had to determine which lead screw/stepper motor combination would work best for our system. This involved finding values such as thrust, torque, backlash, and the lead screws' critical velocity. I also had to take into consideration the accuracy, repeatability, and resolution specifications. Making an excel program and testing many different combinations was the best approach in determining the right choice. I chose a single acting spring return pneumatic actuator because of its slow extension, quick retraction, and low noise characteristics.